The Role of Filtration in the Biopharmaceutical Industry
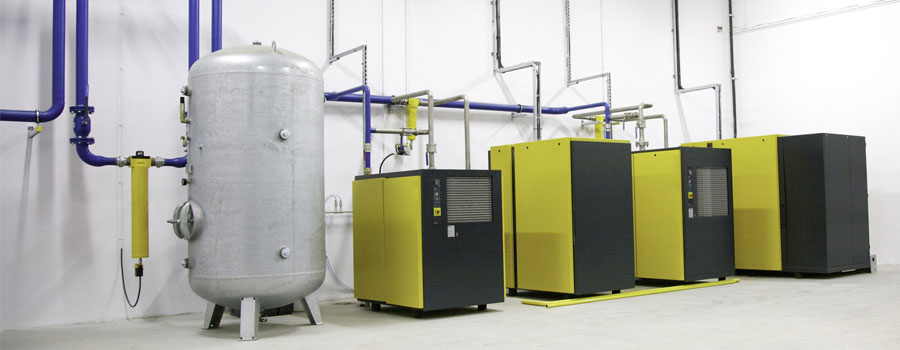
In the pharmaceutical industry, the importance of clean and sterile water cannot be overstated. Almost every stage of the production process, from culture preparation to downstream processing, requires sterile water. To achieve high-quality pharmaceutical products, companies rely on various filter types to effectively eliminate impurities, contaminants and microorganisms from liquids.
However, it is important to meticulously select and implement these filters to meet the industry’s rigorous demands for clean water and guarantee the safety and efficacy of pharmaceutical formulations. This article will delve into the types of filters commonly used in biopharma to ensure optimal water quality and uphold the highest standards in pharmaceutical manufacturing.
6 filter types for pharmaceuticals
The six types of filters commonly used in biopharma include nanofiltration membranes, employed for precise separation; reverse osmosis systems, adept at purifying liquids; ultraviolet purification systems, eradicating microbes; bag filters, proficient in diverse particle capture; ceramic filters, known for their resilience; and self-cleaning filters, offering sustainable maintenance. These filter variants collectively epitomize the pharmaceutical industry’s dedication to meticulous purification, ensuring the integrity and quality of diverse substances.
1. Nanofiltration Membranes
Nanofiltration membranes are a type of pressure-driven membrane that functions by passing water through them under pressure. They are commonly used to separate viruses or heavy metals from water.
The mechanisms involved in nanofiltration membranes include a combination of solution-diffusion, the Donnan effect, electromigration and dielectric exclusion. These membranes offer effective separation capabilities, making them valuable in various applications requiring precise filtration and separation and concentration of specific substances. Nanofiltration membranes are commonly used in situations that require precise filtration and separation of specific substances from water.
2. Reverse Osmosis Systems
Reverse osmosis systems are widely used for water purification in various situations and conditions. They are particularly valuable when removing a wide range of contaminants from water sources, including dissolved solids, salts, minerals, bacteria, viruses and other impurities. Reverse osmosis is commonly applied in water treatment plants to produce clean and safe drinking water from various water sources, such as groundwater, surface water and seawater.
It is also utilized in industries where high-purity water is essential, such as in the pharmaceutical, food and beverage, and electronics industries. Reverse osmosis systems are effective in areas with poor water quality, providing a reliable solution for producing pure and high-quality water for consumption, manufacturing processes and various applications where clean water is critical.
3. Ultraviolet Purification Systems
Ultraviolet purification systems are widely used for water disinfection in various situations and conditions. They are particularly effective in eradicating microorganisms, including bacteria, viruses and protozoa, from water sources. Ultraviolet purification is commonly applied in residential, commercial and industrial settings to ensure safe and clean drinking water.
These systems find extensive use in water treatment plants, swimming pools and wastewater treatment facilities to control the spread of waterborne diseases and to meet stringent water quality standards. Ultraviolet purification is a chemical-free method, making it environmentally friendly and safe for human consumption. It is an essential technology in areas with concerns about water contamination and in regions where access to clean and potable water is critical for public health and safety.
4. Bag Filters
Bag filters are versatile mechanical devices used for filtration in various industries, including the biopharmaceutical sector. They serve as effective tools for purifying both air and water in different situations and conditions.
In water filtration, bag filters are utilized to remove contaminants from water or other fluids. They consist of fabric bags with varying pore sizes that allow water to pass through while trapping particles larger than the pore size. This method is commonly employed in water treatment plants, industrial processes and commercial applications to ensure the purity of water for consumption, manufacturing and other uses.
In the pharmaceutical industry, bag filters play a crucial role in air purification. They are employed to capture dust and airborne particles from the air required for various processes and from the air released during operations. By eliminating dust and contaminants, bag filters help maintain a clean and safe environment, protecting the health of workers and preventing air pollution. Bag filters find extensive use in pharmaceutical manufacturing facilities, laboratories and clean rooms to meet stringent air quality standards and ensure the safety and integrity of pharmaceutical products and processes.
5. Ceramic Filters
Ceramic filters are primarily used for water filtration in various situations and conditions in the pharmaceutical industry. They are specifically designed to remove larger contaminants from water or other fluids, as their pore sizes are not small enough to trap microbes or smaller contaminants effectively. Therefore, ceramic filters are commonly employed to eliminate sediments, particles and larger impurities from water sources. They are particularly useful in areas with poor water quality, where larger contaminants pose a risk to downstream processes and product quality.
While ceramic filters are not typically used as a stand-alone unit for water filtration, they are often used in combination with other filter membranes to achieve maximum filtration efficiency. One of the main advantages of ceramic filters is their relatively low cost, making them a cost-effective solution for water purification in pharmaceutical manufacturing facilities, laboratories and other applications where clean water is essential.
6. Self-Cleaning Filters
Different types of filter membranes suffer from one common problem: the accumulation of the contaminant either on the filter membrane or inside it. This decreases the filter efficiency. As a workaround for this problem, the self-cleaning filters are used. Self-cleaning filters work in different ways according to the filter design.
Self-cleaning filters are particularly valuable in industries where a constant and reliable flow of filtered fluids is critical. They find extensive application in water treatment plants, wastewater treatment facilities and industrial processes where a consistent supply of clean water is required.
Additionally, self-cleaning filters are used in pharmaceutical manufacturing, food and beverage production and chemical processes where maintaining a high level of product quality and purity is essential. However, some common ways by which the self-cleaning filter works are:
- Direct Flushing
In self-cleaning filters, a cleaning fluid, such as water, is directly applied to the accumulated contamination on the filter that effectively washes away these contaminants.
- Back Flushing
In such self-cleaning filters, the fluid flow through the filter is reversed, which helps remove the contaminants from the other side of the filter membrane.
- Automatic Self-Cleaning Filters
Such self-cleaning filters detect the change in the pressure drop across the filter membrane due to the accumulation of the contaminant layer over the filter. When such a change in pressure drop is detected, an automatic scraper fitted in the gap between the filter membrane and the exterior pipe housing is moved, which scraps away all the accumulated contaminants.
What to consider when selecting a filter
When selecting a filter in the biopharmaceutical industry, there are several important factors to consider. These factors include filter material compatibility with the product, pore size selection based on particle retention requirements, validation and regulatory considerations, filter performance characteristics, including flow rate and capacity, and cost-effectiveness.
Filter Material Compatibility
The filter material used should be compatible with the specific product being processed. Different filter materials can have varying interactions with the product, which may result in the adsorption or leaching of substances that could potentially impact the quality or safety of the final product. To ensure compatibility, it is suggested to conduct thorough compatibility testing and evaluate any potential interactions between the filter material and the product. This helps select the filter material that is chemically compatible and minimizes any risks associated with interactions.
Pore Size Selection
It is important to select an appropriate pore size to achieve the desired level of particle retention during filtration. The pore size should be determined based on the size of particles that need to be removed or retained. Factors such as the nature of the product, particle size distribution and regulatory requirements should be considered when determining the optimal pore size. By choosing the correct pore size, the filter can effectively remove contaminants while allowing the desired components of the product to pass through.
Validation and Regulatory Considerations
Filters used in the biopharmaceutical industry must meet regulatory requirements and be part of a validated filtration process. It is important to source filters from reputable manufacturers who provide comprehensive validation data and regulatory documentation. Regulatory agencies, such as the FDA or EMA, often have specific guidelines and requirements for filter selection and validation. Adhering to these guidelines ensures compliance and helps guarantee the safety, efficacy and quality of biopharmaceutical products.
Filter Performance Characteristics
The performance characteristics of the filter, including flow rate and capacity, play a significant role in the filtration process. The flow rate refers to the rate at which the product passes through the filter.
It is essential to optimize the flow rate to ensure efficient processing without compromising filtration performance. The capacity of the filter pertains to its ability to retain particles over a specified period. Selecting filters with appropriate flow rates and capacities ensures that the process requirements are met while maintaining the desired level of particle retention and product quality.
Cost-Effectiveness
Evaluating the cost-effectiveness of filters involves considering various factors. The initial cost of the filter, the frequency of filter replacement and the overall impact on process economics must be assessed. While ensuring high-quality filtration is paramount, it is necessary to strike a balance with the cost implications. By weighing the cost of the filter against its performance and durability, biopharmaceutical companies can make informed decisions that maximize the efficiency and profitability of their filtration processes while maintaining product integrity.
Conclusion
In conclusion, the eight filter types explored above play pivotal roles in diverse industries, ensuring the purification and separation of substances in water and air. Nanofiltration membranes are vital for precise filtration and separation, while magnetic filters efficiently remove iron particles from fluids. Reverse osmosis systems excel in water purification, and ultraviolet purification systems effectively disinfect water by eliminating microbes.
Bag filters are versatile tools for both air and water purification, and ANFDs facilitate the filtration, washing and drying of solid substances. Ceramic filters offer cost-effective water filtration, and self-cleaning filters ensure continuous and efficient operation. Each filter type possesses unique capabilities, making them indispensable for meeting stringent quality standards and enhancing processes in various applications.
Avantor offers process filtration system products for biopharma production. From nanofiltration membranes and magnetic filters to reverse osmosis systems and ultraviolet purification systems, we ensure the highest standards of purity and efficiency with our reliable filters and purification systems.